.
Real airplane, the fan is in the front, the little wheel is in the back. That is, if it has a little wheel. Started out, we just had a skid. Nowadays, lotsa folks frown on skids. But if you're into Flying On The Cheap there's a lot to be said for a skid.
The main purpose of putting anything in the back is to keep the tail off the ground. If that's all you want to do, you use whatever works. Skid works.
Most folks incorporate some form of energy absorption mechanism in whatever works; that thing that keeps the tail from hitting the ground. Piecea wood works. Pivot the piecea wood in the middle, wrap some shock cord forward of the pivot, when the thing hits the ground it won't break. Kinda springy. Sorta like a spring, which also works. Leaf spring, like one offen a car. Or a wagon, if it's a small wagon. Fiberglas works too. Or you can use a piecea wood. Ash works good. Hickory too. (Ask for a sledge hammer handle. In a pinch, you can use a shovel handle. In fact, a popular homebuilt from the 1930's used the curved portion of a shovel handle for a tail skid.)
The bad thing about using a steel spring in back is the sparks. Looks kinda neat, taxi'ing at night, little shower of sparks behind you. Not on grass, of course but over at Palomar or Oceanside. More fun at Palomar because they got a tower and you know how much folks love sparks when they live in towers.
Or you can use a piecea wood, put a little metal shoe on the end. Best of both worlds: Cheap, easy to make piecea wood, with a couple wraps of shock cord. (You can get some at Home Dee Pot.) Plus, you got this steel shoe, gives you a nice shower of sparks when the tail comes down, causes Tower Dwellers to shine their red light at you and say funny stuff on the radio. Almost as much fun as landing on the taxi way. (I have a lot of trouble remembering my hull number, usually just add five to the last one I heard. Seems to work okay.)
Have you seen them white plastic cutting boards? I've been using them for fair-leads. Slippery stuff.
I'll bet you could put a piece of white plastic cutting board on your tail skid, cause it to stop sparking and start sliding. Not very handy at Ranchita, though. In fact, that's why you have a steel shoe back there, so's you can come to a stop before you hit the windmill. No, you can't go there, it ain't a runway, it's a road. Graded it nice & smooth after the Pines fire took care of the brush. Seven hundred foot of road. Only folks that use it is me and a lot of dope smugglers. That metal shoe works a treat on dirt. Not too many sparks. But some. Guess I'd better put on a wheel.
Little wheel. Harbor Freight. It thought it was a caster until I got aholt of it. Sez ‘88x31' molded into the rubber. Or urethane. Or whatever. Ball bearing. Three-eights bore. Made up a tail-wheelie-thingee outta some tubing, couple of bronze bushings. Zerk fitting. Horn bolts on. Don't weigh much but it's heavier than a piecea wood and three feet of shock cord. Hell of a moment, too. Seventeen feet four and three-quarters inches times four point three seven pounds, plus the spring... means I have to move the whole gawdamned engine forward about 1.375 inches just so's I can have a little wheel in back. Or bolt about ten pounds of lead to the oil cooler. (Rather move the engine.) Now I gotta find some sort of spring.
Looked around for a steel spring but couldn't find one I could afford. Checked with the EAA experts and was told I could find leaf springs in any junk yard. One EAA expert told me to look for a Model T, take the spring offa that. ( When was the last time you saw a Model T in a junk yard? Where do they get those people?) These are the same experts who think the Spruce Goose is made outta spruce and that an AN3 is 3/16". I guess they don't get out much.
Ever heard of a camber compensator for swing-axle Volkswagens? It's a steel spring shaped about like an archers' bow except with angles instead of curves. Bolts to a pivot on the bottom of the tranny with the ends of the spring out toward the wheels, pressing up on the axles. Works. Sorta. First used it on the Porsche, way back When. Spring is about an inch and an eighth for bugs, inch and a half for buses. New, they want the earth for the thang but used, at the swap meet, over where all the air-cooled Volkswagen owners get together, you pick one up for a twenty dollar bill.
One camber compensator makes two tail wheel springs. Pretty good tail wheel spring, too, cept it's kinda soft. And at twenny bucks, expensive for someone Flying On The Cheap. (Yes, I got a couple of them. But you don't. And the Flying On The Cheap thingee is really for you, not me.)
Harbor Freight, that's the ticket. Go prowling around. They leave you alone in Harbor Freight. Go to Home Dee Pot there's always some idiot asking if they can help you. So you ask, "Double headed nails?" and they give you a silly smirk as if you've just dropped in to practice your humor. Real hardware store carries crockery and dynamite and knows what you mean when you ask for five pounds of eight-penny double headed nails. Home Dee Pot only seems to have these perky idiots offering help they can't provide.
So I go prowling around Harbor Freight and find the Perfect Tail Wheel Spring. Looks like a pry bar but it's really a tail wheel spring. Or soon will be.
Yes, I made some drawings. They'll eventually go up with the other ' stuff. And I'll take some pictures too, soon as Santa comes around (I've been saving up for a digital camera.) Then I'll have me a regular tail wheel, like all the yuppies use.
But I'm gonna miss them sparks. And blowing the tail around. And getting the Tower Dwellers all excited. Mebbe I'll send them over to Home Dee Pot, tell them to ask for redwood plaster lath. Regular snipe hunt, seeing all them yuppie-type clerks running around trying to figger out what Redwood Plaster Lath might be and if they got some and where it might be hidden if they do. Wasn't like that at the old hardware store. "Gimme ten sticks of twenty percent Hercules, twenty caps and five foot of fuse, please." And they'd write it up and ask you was there anything else. Shoulda stocked up on wooden plaster lath when I had the chance.
-R.S.Hoover
-Sept 2003
Flying, homebuilt airplanes, working with wood, riveted aluminum, welded steel tubing, fabric, dope and common sense. Gunsmithing, amateur radio, astronomy and auto mechanics at the practical level. Roaming the west in an old VW bus. Prospecting, ghost towns and abandoned air fields. Cooking, fishing, camping and raising kids.
Monday, November 27, 2006
AV - Wing Design
> Is there a common percentage that the front wood (or box) spar is placed > from the leading edge, say on high wing airplanes like the Piper Cub, or > Aeronica.? >
-------------------------------------------------
It depends largely upon the designer and the mission or role of the aircraft.
Col. Virginius Clark (U.S.Army Air Corps) created a defacto light-plane standard for his family of airfoils (USA-35b, as used by Taylor in the design of the Cub [USA = U.S.Army], plus the entire Clark-x series, upon which the NACA Four-Number Series (ie, 4415, etc) is based.
Clark found that for strut-braced, fabric covered wings using wooden spars, positioning the spars at approximately 15% & 65% of the chord (measured from the leading edge) provided the best ratio of strength to weight.
This ratio (and Clark's airfoils) would apply to the two samples you've cited. But Clark's spar spacing also proved to scale rather well. Many earlier designs (ie, prior to about 1923) when re-engineered with a 'Clark wing' usually shed quite a few pounds and enjoyed significant gains, not only in climb but cruise performance. (Lindy hopped the pond under a 'Clark wing.')
-R.S.Hoover
-------------------------------------------------
It depends largely upon the designer and the mission or role of the aircraft.
Col. Virginius Clark (U.S.Army Air Corps) created a defacto light-plane standard for his family of airfoils (USA-35b, as used by Taylor in the design of the Cub [USA = U.S.Army], plus the entire Clark-x series, upon which the NACA Four-Number Series (ie, 4415, etc) is based.
Clark found that for strut-braced, fabric covered wings using wooden spars, positioning the spars at approximately 15% & 65% of the chord (measured from the leading edge) provided the best ratio of strength to weight.
This ratio (and Clark's airfoils) would apply to the two samples you've cited. But Clark's spar spacing also proved to scale rather well. Many earlier designs (ie, prior to about 1923) when re-engineered with a 'Clark wing' usually shed quite a few pounds and enjoyed significant gains, not only in climb but cruise performance. (Lindy hopped the pond under a 'Clark wing.')
-R.S.Hoover
VW - Lube Jobs, Needles and Looking Kewl
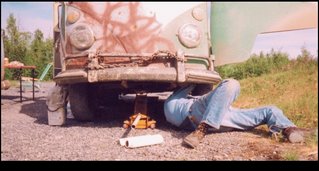
I shouldn't be writing this. I shouldn't have to be writing this, since it covers a topic everyone already knows. Or should. But here goes.
Like most of my articles, this one began with a message from a youngster, the proud new owner of a old beetle. He'd found the 'sermon' files and sent me a message that, aside from the question it contained, told me he hadn't read any of the available manuals. I answered his question and, being the sweet sonofabitch I am, I pointed him toward the books and told him to get hot -- I didn't have time to answer questions he could answer for himself.
Usually, that's all it takes to stub the tender ego of youth -- I didn't expect to hear from him again. But I did.
Okay, he sez, he's got the manuals. And he's impressed. He has the Bentley, the Muir and the Haynes and he's reading as fast as he can and if I had the time, would I please tell him how much grease he should put in his fittings when he gives his '64 bug a lube job. It squeaks, he sez.
Instead of telling him, I pull out the manual, to point him toward the proper page and paragraph. But it wasn't there. Haynes says only to grease the thing -- no mention of how much. Muir sez the same thing, except they screw things up by passing out bum dope on what to do about a bad Zerk fitting(*). The Bentley manual does a little better, saying "Continue with the greasing until fresh grease begins to emerge from the lubrication points." (Page 8-8 in the Bentley book for bugs.) So I tell him where to find it and get back to doing what I was doing, which has to do with propane and computers and all kinds of neat stuff.
Back comes another message, quick like a bunny. It's a Yeahbit message: "Yeah, I read that... but that takes something like twenty strokes and all of my friends say that's 'way too much."
Ah yes -- peer pressure, and the deadly need to look kewl. This fellow's friends, one or two of whom might own a Volkswagen, were giving him the benefit of Conventional Wisdom. And then there's the Muir manual, which sez to stop greasing as soon as you see grease come out. Wrong.
I sent the kid a long, carefully worded message explaining that the purpose of a lube job is to replace the chassis lube, offering him some tips on how to keep things greasy so they'll last a long time. The kid fires right back to say that after sending his second message he's checked with his dad and the local quickie-lube emporium (shudder) and everybody agrees... one or two squirts of grease is all you need. He also had some rather sharp things to say about lube needles. (see below) Faced with the possibility of looking un-kewl, the kid had taken the easy way out.
Good-bye, kid. Good luck in the contest.
I go back to playing with vaproizers and trying to figure out how to fit a one hundred sixty liter propane tank in a bus and I'm laying out there under Grendel, looking at a patch of blue sky through her 'good condition' cargo bay when I begin to wonder.... doesn't everybody know the whole idea is to change the lube rather than just add a bit?
Lube Change vs Oil Change
A lube job is in fact the replacement of the lubricating grease, not just its replenishment.
Lubricants -- oils, greases and soaps -- literally wear out. Their long-chain molecules are sheared by heat and pressure and over time they become contaminated with moisture, dust -- and in the case of engine oil, with combustion products. We deal with worn-out, contaminated lubricants by replacing them.
Everyone knows they have to change their oil rather then just topping-up. And most of us know we have to change our tranny-lube every couple of years. And we scrub all the old grease out of our wheel bearings and the spindle bore and repack them with new grease...
So what's different when it comes to chassis lube? A lube-job is just another form of oil-change.
When doing a lube-job, too make sure you do a proper job of it, you keep pumping until you see the new grease coming from the part. Yeah, it's a mess -- the old grease gets all over everything. You put down some newspaper or something else disposable to catch the globs of falling grease, and use paper toweling to wipe any any grease that clings to the part. When you're done, you should put a cap of some kind over the Zerk fitting. Cars used to come with neat little rubber caps for this job, and replacements were commonly available, although I haven't seen their like in recent years. Instead, I've taken to molding aluminum foil over the Zerks after every lube-job.
Lube jobs, like oil changes, are not carved in stone -- you can't just go by miles traveled or a set period of service, you need to pay attention to the type of miles traveled and the conditions encountered during a given period of service. Normally, your steering and front suspension needs its lube replaced about every six thousand miles -- that's the spec. Then comes the fine print. Rough roads? (meaning lots of action from the suspension) -- replace the lube more often. Dusty roads? (meaning more contaminants, plus the wicking-effect of dust) -- replace your lube more often. (Oddly enough, a vehicle that does not drive very much needs its lube replaced more often than one which does.) It's all there in the manuals (at least, in most of them :-). And has been, for about seventy years.
Keep it greasy, it lasts longer.
It is not just proper lubrication that prolongs the life of the vehicle, there is also the implied cleaning that accompanies any lube-job. Dirty, dusty or harsh conditions, you need to clean your undercarriage more often. That's what you do before you change the lubricant, just as you clean off your engine when do an oil change.
Long, Boring (but real) Example
A fair example of the frequency at which you may need to change your lube was the run to Inuvik last year. Round trip, it was only eight thousand miles but there were so many miles of dusty, unpaved road I thought it best to double-up on my lube jobs, doing the greasy chore three times during the trip.
I've even got the photos to prove it :-)
Following the trip to Inuvik I ran down to Cabo as a preliminary for our up-coming 12 July trip. I had the bad luck to run into the tail-end of a hurricane and had to ford a number of flooded vados. Soak your bus in water, you gotta change the engine oil, tranny lube and chassis grease. All tolled, the bus enjoyed five lube jobs for only fifteen thousand miles of service. (There was a three-thousand mile run to Kansas City in there somewhere.)
Doing the Deadly Deed
There are many different types of grease. For most chassis lubrication needs any good grease will work but see your manual for their recommended specifications. For CV's you want a different formualtion than the grease you use for your torsion bars-- one more suitable for high pressures. But CV lube is great stuff for tie-rod ends and ball joints.
There are three basic types of manually-operated grease guns but all of them are in fact a form of hydraulic pump, designed to pump grease rather than oil. The lever-type gun can usually generate about 3000 psi, more than enough to force the thick grease into the finest fitting.
It is common practice to maintain a different grease gun for each type of grease your vehicle requires. I use a moly-based grease for CV's, tie-rods and ball-joints, a lithimum-based grease for the torsion-bar and steering knuckles.
Grease is sold in convenient cartridges, although you can bulk-load your gun if you wish. Wheel-bearing grease is normally sold in cans. The best wheel-bearing grease has very long molecules -- it's called 'long-fiber' grease -- and is unsuitable for use in manual grease-guns. Each cartridge holds about 400 grams of grease -- about fourteen ounces. It takes about eight ounces of grease to do a proper job on an old bus. Later model buses have fewer fittings -- more 'Lifetime-lubricated' parts waiting to fail -- and so takes less grease per job. On the Inuvik run I used two tubes of grease and had to replace one Zerk, apparently kissed by a rock.
Zerks! Zounds! and Needles
A Zerk fitting is a nipple shaped to match the nozzle of a grease-gun. The grease passage through the nipple is closed with a check-valve, a tiny steel ball supported by an equally tiny spring. Left exposed, Zerk fittings go bad quite quickly which is why they should always be protected with a cap.
Being a lubricated joint, tie-rod ends were once fitted with Zerk fittings and many still are. The same is true of ball-joints. Unfortunately, it has become common for auto-makers to equip their products with ball-joints and tie-rod ends that are 'lubricated for life,' which is automotive double-speak meaning the things will only last about sixty thousand miles before they must be replaced due to lack of lubrication. They'll last longer if you stick to smooth, paved roads but the bottom line is that you can't lubricate them, meaning they'll wear-out faster than a fitting you CAN lubricate.
The solution to this 'Lifetime Lubrication' bullshit is pretty simple. Some VW ball-joints have a threaded hole for a Zerk fitting. Simply replace the nylon plug with a Zerk and pump away -- your ball-joints will love you for it. Another, less effective method, is to inject grease directly into the fitting through the rubber boot, using a large hypodermic needle. I know it sounds crazy but it works. Indeed, it sounded so crazy that the kid mentioned above had never heard of it nor had any of his friends. Thanks to Conventional Wisdom the kid was convinced the suggestion -- and all of my articles -- had no value, that I was just another geezer blowing smoke up his ass. And besides, his dad told him it was illegal to own a hypodermic needle(!!!).
Ah well.
Wanna nice big hyperdermic needle? Go down to your FLAPS and buy one. It will be hanging on the wall in a blister pack, somewhere near the grease-gun stuff. Plews (brand name) makes one -- their catalog number is 05-037. Cost about three bucks. Cheep! (This is also how you get those extra miles out of your CV joints.)
The 18 gauge hypodermic needle, which at least in California is perfectly leagal to own, is swaged to... you guessed it -- a Zerk fitting! Plug it into the nozzle of your grease gun, stab the needle through the boot of your tie-rod end, CV or ball-joint, and pump away. Yeah, it makes a hole, and yeah, some of the grease will leak out. But the thing will last a lot longer, too.
--Bob Hoover
(*) So how did Muir screw-up on his lube-job instructions? First, he sez to pump until you see the grease come out -- "...indicating that it is full." All that does is top-up the old grease. You want to CHANGE the grease, not just top it off. Keep pumping until you see NEW grease coming out.
Secondly, he sez that if you have a bad Zerk, run down to a service station and have the kid use the pneumatically-powered grease-gun to force grease through the fitting.
Bad, bad idea. What if the fitting is filled with dirt? What if the spring has failed and the ball is rusted in place? (Hint: You'll pump parts of the spring into the joint you're trying to lubricate.) And finally, what if even the powered grease-gun can't force grease through the nipple?
If you have a bad Zerk fitting, replace it. You can buy Zerk fittings at any auto-parts place that sells grease -- they come with the territory. You should keep a couple spare Zerks of each type (they come in both straight and angled flavors) in your tool kit, just as you keep a few spare fuses and a few spare tire-valve cores. It's not anything special, it's what mechanics DO.
In all fairness, the Muir manual mentions replacing Zerk fittings... but only when they fail to make an adequate seal with the nozzle of the grease-gun.
There's a bit more to it than that. -- rsh
VW - Oil Bath Aircleaner
George,
You have been misinformed as to the principle of the oil-bath air-cleaner. There is no vaporization and condensation of the oil bath. I suppose horsehair may have been used for an air filter by someone but it was not Volkswagen.
The oil-bath air-cleaner is a classic example of a two-stage' kinetic filtering element, removing virtually all particulate contaminants from the air at all engine speeds.
Incoming air is forced to follow a vertical descending path toward the pool of oil then drawn upwards. Having a mass several million times that of a molecule of air, the inertia of the dust particles makes it impossible for them to follow the abrupt change of direction in the air-stream, causing the particles to strike the pool of oil where they become trapped. This works best at high rates of air-flow.
The coir filter element, which forms what is termed a 'labyrinth filter', applies the same principle but in a different manner. The coir element forces the air to change direction many times. The fibers are coated with kerosene. Dust particles collide with the fibers and are trapped by the kerosene.
The spec for cleaning the coir filter is to immerse it in kerosene, allowing it to soak for up to half an hour. It is then sloshed repeatedly and allowed to drain. This was done twice a year under normal driving conditions, as often as deemed necessary under dusty conditions.
In use, particles of dust trapped in the oil bath cause the level of the oil to rise. Under severe conditions it may require cleaning on a daily basis. (Moisture does the same thing. In a rainy climate it isn't unusual for the air cleaner to accumulate a quart of water per month.)
Under Volkswagen's original apprenticeship training program the effectiveness of the oil-bath air-cleaner was demonstrated by removing the sludge from a the oil-bath and coir filter, flushing it with solvent and examining the residue. A low-power microscope was needed to observe the smallest particles.
The same principle is used to clean the air for large stationary engines and for air conditioning applications, in which a recirculating water-bath may be used instead of oil, and the air may be forced past as many as two dozen up-down baffles, removing even microscopic particles of low density such as pollen. In some systems the water-bath is sealed with a thin film of mineral oil. Trapped particles fall thru the oil and are removed by the recirculation of the water beneath the oil film. I understand special silicone-based oils are used in modern HVAC systems but non-human applications such as large stationary engines continue to use mineral oil. Residential HVAC systems typically use labyrinth-type filters, designed primarily to catch fibers rather than particles.
Paper and foam filtering elements are based on the labyrinth principle. The effectiveness of the oil-bath air-cleaner is superior to that of the typical paper or foam filtering element. Paper air-filtering elements came into use when they became effective at trapping particles of a certain size. Oil-bath filters will trap smaller particles but there is no evidence of accelerated engine wear for particles below a certain critical size.
Air filters for rough service (armored vehicles, farm machinery, etc) where an oil-bath would be unsuitable, and high-volume applications (turbines, etc) use the same physical principle of mass-differentiation, typically drawing the air through several stages of centrifuging during which the greater mass of the dust particles causes them to be separated from the air-stream. Although such air-cleaners may be powered or static, they are often called 'turbo' air-cleaners. They are often used in conjunction with disposable labyrinth-type filters. For Volkswagen owners running off-pavement, the static type of 'turbo' air-cleaner used on Ford tractors has proven most effective.
Recent air-pollution legislation enacted here in California requires automotive paint shops to reduce their emission of vapor and particulate material. I mention this because the most cost effective means of doing so involves the use of high-volume, low-pressure spray-painting systems in conjunction with a multi-baffle water-bath air-cleaner that uses exactly the same principle as the air-cleaner on an early Volkswagen.
-Bob Hoover -4 May 1997
You have been misinformed as to the principle of the oil-bath air-cleaner. There is no vaporization and condensation of the oil bath. I suppose horsehair may have been used for an air filter by someone but it was not Volkswagen.
The oil-bath air-cleaner is a classic example of a two-stage' kinetic filtering element, removing virtually all particulate contaminants from the air at all engine speeds.
Incoming air is forced to follow a vertical descending path toward the pool of oil then drawn upwards. Having a mass several million times that of a molecule of air, the inertia of the dust particles makes it impossible for them to follow the abrupt change of direction in the air-stream, causing the particles to strike the pool of oil where they become trapped. This works best at high rates of air-flow.
The coir filter element, which forms what is termed a 'labyrinth filter', applies the same principle but in a different manner. The coir element forces the air to change direction many times. The fibers are coated with kerosene. Dust particles collide with the fibers and are trapped by the kerosene.
The spec for cleaning the coir filter is to immerse it in kerosene, allowing it to soak for up to half an hour. It is then sloshed repeatedly and allowed to drain. This was done twice a year under normal driving conditions, as often as deemed necessary under dusty conditions.
In use, particles of dust trapped in the oil bath cause the level of the oil to rise. Under severe conditions it may require cleaning on a daily basis. (Moisture does the same thing. In a rainy climate it isn't unusual for the air cleaner to accumulate a quart of water per month.)
Under Volkswagen's original apprenticeship training program the effectiveness of the oil-bath air-cleaner was demonstrated by removing the sludge from a the oil-bath and coir filter, flushing it with solvent and examining the residue. A low-power microscope was needed to observe the smallest particles.
The same principle is used to clean the air for large stationary engines and for air conditioning applications, in which a recirculating water-bath may be used instead of oil, and the air may be forced past as many as two dozen up-down baffles, removing even microscopic particles of low density such as pollen. In some systems the water-bath is sealed with a thin film of mineral oil. Trapped particles fall thru the oil and are removed by the recirculation of the water beneath the oil film. I understand special silicone-based oils are used in modern HVAC systems but non-human applications such as large stationary engines continue to use mineral oil. Residential HVAC systems typically use labyrinth-type filters, designed primarily to catch fibers rather than particles.
Paper and foam filtering elements are based on the labyrinth principle. The effectiveness of the oil-bath air-cleaner is superior to that of the typical paper or foam filtering element. Paper air-filtering elements came into use when they became effective at trapping particles of a certain size. Oil-bath filters will trap smaller particles but there is no evidence of accelerated engine wear for particles below a certain critical size.
Air filters for rough service (armored vehicles, farm machinery, etc) where an oil-bath would be unsuitable, and high-volume applications (turbines, etc) use the same physical principle of mass-differentiation, typically drawing the air through several stages of centrifuging during which the greater mass of the dust particles causes them to be separated from the air-stream. Although such air-cleaners may be powered or static, they are often called 'turbo' air-cleaners. They are often used in conjunction with disposable labyrinth-type filters. For Volkswagen owners running off-pavement, the static type of 'turbo' air-cleaner used on Ford tractors has proven most effective.
Recent air-pollution legislation enacted here in California requires automotive paint shops to reduce their emission of vapor and particulate material. I mention this because the most cost effective means of doing so involves the use of high-volume, low-pressure spray-painting systems in conjunction with a multi-baffle water-bath air-cleaner that uses exactly the same principle as the air-cleaner on an early Volkswagen.
-Bob Hoover -4 May 1997
VW - Dim 6v Headlightss
> Do I need to convert to 12V for bright lights?
---------------------------------------------------------------------------
Definitely not.
Six volt lights are just as bright as 12v lights. Or 24v lights, for that matter.
The problem is that the voltage loses due to accumulated corrosion are proportionally greater on low-voltage systems. That simply means you need to devote more time to your maintenance procedures.
Cleaning your contacts will cause a definite improvement but most of the corrosion (and thus most of the losses) will be in the switch and in the ground return path. In the VW many of the ground path connectors were riveted rather than spot-welded. Over time, corrosion builds up around the rivet -- often under the paint and completely invisible on inspection. Not only are such bad connections difficult to locate, they can be difficult to repair in that you need to get back to bare metal to ensure a low-resistance connection.
In the VW sedan, complaints of dim lights can often be traced to a high resistance ground path between the fenders and the body (!) That's because the grounding terminal for the head or tail-lights is attached to the fender... which is then bolted to the body. Providing a low resistance ground path in the form of a jumper from the light fixture to the body is often the best solution.
Converting to 12v usually results in brighter lights but it does not address the root problem. (It's a bit like taking a pain-killer when you have cancer -- you may feel better but it doesn't cure anything :-)
-Bob Hoover
---------------------------------------------------------------------------
Definitely not.
Six volt lights are just as bright as 12v lights. Or 24v lights, for that matter.
The problem is that the voltage loses due to accumulated corrosion are proportionally greater on low-voltage systems. That simply means you need to devote more time to your maintenance procedures.
Cleaning your contacts will cause a definite improvement but most of the corrosion (and thus most of the losses) will be in the switch and in the ground return path. In the VW many of the ground path connectors were riveted rather than spot-welded. Over time, corrosion builds up around the rivet -- often under the paint and completely invisible on inspection. Not only are such bad connections difficult to locate, they can be difficult to repair in that you need to get back to bare metal to ensure a low-resistance connection.
In the VW sedan, complaints of dim lights can often be traced to a high resistance ground path between the fenders and the body (!) That's because the grounding terminal for the head or tail-lights is attached to the fender... which is then bolted to the body. Providing a low resistance ground path in the form of a jumper from the light fixture to the body is often the best solution.
Converting to 12v usually results in brighter lights but it does not address the root problem. (It's a bit like taking a pain-killer when you have cancer -- you may feel better but it doesn't cure anything :-)
-Bob Hoover
VW - Retard on #3 Cylinder
>I've heard guys talk about this retard business before but I've never seen
>anything official on it.
-------------------------------------------------------------- '
Workshop Manual for Volkswagen Transporter, 1963-1967' ISBN 0-8376-0391-9 Section E-9, page 12 'Service Note: From 3rd August 1964, Chassis No. 115 000 001, Engine No. 8 788 071, all VW engines are fitted with modified distributors. The breaker cam lobe which controls the firing point of No. 3 cylinder is offset 2 distributor-shaft degrees in the retarded direction.'
Various other associated Notes, Warnings and Illustrations, bleeding over to page 12a, the obverse of which is blank, indicating 12a is a supplement, inserted after normal pagination of the manual.
(To find out when they stopped using the retard, you need to look in a Factory Service Manual covering the 1971 model year.)
If you have a VW engine of 1200cc displacement or more and you are using the original upright oil cooler then you should be using a distributor which retards the #3 cyl. firing point.
If you are using an engine fitted with a dog-house type oil cooler it doesn't matter what type of distributor you are running, although one without the retard will improve the engine's efficiency.
If you have a distributor of unknown provenance and wish to determine if its #3 lobe is retarded, you can develop that information by inspection, either with a distributor diagnostic machine or by installing the distributor on an engine fitted with a degree wheel and observing the firing point OF each cylinder using a stroboscopic timing light. Two degrees at the cam is four at the crank so it's pretty easy to spot.
Normal service life of the VW distributor is 50k to 70k miles and is determined by end-float. That means even the youngest of the retarded distributors was worn-out by about 1985.
-Bob Hoover
>anything official on it.
-------------------------------------------------------------- '
Workshop Manual for Volkswagen Transporter, 1963-1967' ISBN 0-8376-0391-9 Section E-9, page 12 'Service Note: From 3rd August 1964, Chassis No. 115 000 001, Engine No. 8 788 071, all VW engines are fitted with modified distributors. The breaker cam lobe which controls the firing point of No. 3 cylinder is offset 2 distributor-shaft degrees in the retarded direction.'
Various other associated Notes, Warnings and Illustrations, bleeding over to page 12a, the obverse of which is blank, indicating 12a is a supplement, inserted after normal pagination of the manual.
(To find out when they stopped using the retard, you need to look in a Factory Service Manual covering the 1971 model year.)
If you have a VW engine of 1200cc displacement or more and you are using the original upright oil cooler then you should be using a distributor which retards the #3 cyl. firing point.
If you are using an engine fitted with a dog-house type oil cooler it doesn't matter what type of distributor you are running, although one without the retard will improve the engine's efficiency.
If you have a distributor of unknown provenance and wish to determine if its #3 lobe is retarded, you can develop that information by inspection, either with a distributor diagnostic machine or by installing the distributor on an engine fitted with a degree wheel and observing the firing point OF each cylinder using a stroboscopic timing light. Two degrees at the cam is four at the crank so it's pretty easy to spot.
Normal service life of the VW distributor is 50k to 70k miles and is determined by end-float. That means even the youngest of the retarded distributors was worn-out by about 1985.
-Bob Hoover