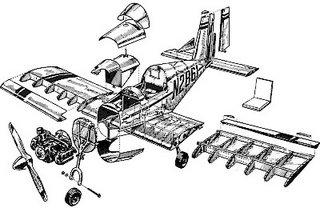
What's a rivet?
Silly question. Everyone knows rivets are those little metal jobbies that hold things together.
Why do you want to hold things together?
Boy! Talk about dumb! Because we don't want them to fall apart, that's why!
Why would they fall apart?
And about there you realize the idiot may know more about stress analysis than you do. Because it's the stresses that make things fall apart and it's rivets that prevent that from happening.
In that ultra-simplistic approach you can think of rivets as stress- or load-paths. When you start thinking of them in that context you will immediately see that the size and type of rivet you use starts to make a lot of sense, along with how many of them you use.
For example, let's say you're up there kicking the bird around and you fall out of a loop a bit too near the ground. To recover you really have to haul on it and end up pulling maybe 3 g's. That means your 650 pound airplane weighed about a ton (!) before you got things straightened out.
The T2's wing has an effective lifting area of about 53 square feet. 2000 pounds divided by 53 is 37.73... nearly forty pounds per square foot.
Out near the tip of your wing the ribs are 18" apart. The spars are about two feet apart so that means some panels of your wing skins have three square feet of surface. Pulling out of that dive, that three square foot panel had to support about 120 pounds.
That's when you begin to wonder, how strong is a rivet? And how many will it take to support 120 pounds?
Would you believe one rivet?
Steel pop-rivets, 1/8" diameter, can safely carry nearly 300 pounds if the load is in shear, meaning the pull is sideways to the rivet.
The truth is, most of the rivets in your wing skins aren't there because you need the strength, they are there to maintain the streamlined shape of the airfoil. If that comes as a surprise, consider the thousands of airplanes that have flown with nothing but a layer of fabric glued to their wooden ribs.
Actually, I'm swinging the lead a bit here because the chord-wise distribution of lift is not uniformly. About half of the load appears in the leading third of the wing and even in fabric-covered aircraft the leading edge is usually something other than fabric.
The point of all this is to quell the doubts many associate with plain old garden variety pop rivets. In the case of the Teenie Two the specified zinc plated steel rivets are more than strong enough.
Just to play the Devil's Advocate, let's take another look at those wing skins and the pop rivets securing them to the ribs and spars. They're spaced about 2" apart out on the ends of the wings. If we leave the spars out of the equation we have a piece of aluminum having an area of three square feet fastened with about 24 rivets. If you assume each rivet can only carry just 100 pounds you will still have enough fastening strength for a load of 2400 pounds. And the 3.5g load was only 120. So you're really pretty safe. In fact, you could use countersunk aluminum pop rivets for your skins and still have a significant safety margin. Save yourself some weight, too. (But only in the skins, please.)
After the load is picked up by the skin it is dumped into to the spars. And after the load is in the spars we have to start calculating the moment of the load as well as its magnitude. If you calculate the load for each inch of the spar's length, you'll see that the caps - the extrusions - are carrying some pretty good stresses. The flush-head aluminum poppers work fine for the skins but the spar has to bear some significant stresses without buckling so you'll want to stick with the 1/8" steel pop rivets. Or something equally strong.
- - - - - - - - - - - - - - - - - - - - - - - - - - - - -
So why did Cal call out 1/8" steel popper for just about everything? Probably because of the convenience. Cal designed the Jeanie's Teenie in the mid-1960's to be built from materials available in any small town. Back then, everyone sold button-head pop rivets and most lumber yards and hardware stores carried various alloys of sheet aluminum in 3'x6' sheets. If you designed a plane to be built using only what's available from your local hardware store then poppers would be the most appropriate choice for fasteners. And zinc or cadmium plated poppers are actually pretty smart in engineering terms because that thin plating of zinc or cadmium is a lot closer to aluminum on the electrolytic scale than is bare steel, stainless steel or Monel. (The closer the elements on the scale, the less electrolytic action between them, thus the less chance of corrosion.)
As further protection against corrosion and as a means of sealing the rivet, Cal said to dip each rivet in anti-corrosion paint from Sears. Unfortunately, he failed to mention the need to wash them first in MEK or lacquer thinner. Such washing is the standard practice when using any rivet that is to receive some form of sealant, since all rivets arrive from the factory with traces of lubricant left over from the manufacturing process. So you rinse it off. So the sealant will stick. (Cal obviously rinsed his rivets before dipping because the original Teenie Two spent most of a quarter-century outside in the weather without any evidence of rusty rivets.)
- - - - - - - - - - - - - - - - - - - - - - - - - - - - - -
If you have a shop filled with riveting equipment and know how to use it, the odds are you'd do exactly that when building a Teenie Two, saving yourself both time and money. And you would probably say as much, from time to time, poking a bit of fun at the newbies who spend more for pop-rivets than you spent on the whole damn airframe :-) (T2 isn't a big bird. Sans engine and landing gear, you're only looking at about a hundred pounds of aluminum.) Or you might point out that using one size and type of fastener (although different lengths) throughout the airframe is not a good example of optimized design. All of which is liable to cause Mr. Newbie to think there is some inherent flaw in using poppers.
There isn't; not when we're talking Teenie Two's. So relax. Properly installed, they work just fine and have for more than forty years in several hundred T2's built in every country except Gondawandaland.
The use of poppers may not reflect optimized design but you should have already guessed that when you saw that Cal used just two thickness of aluminum for everything, notched his ribs instead of fluting them and managed to build the entire airframe without using a single lightening hole. Clearly, this is not an optimized design. But it is an excellent example of appropriate design for an airframe meant to be built by persons having minimum tooling, zero sheetmetal experience and using locally available materials. (Available back then, anyway.)
If you're building a T2 and don't have a lot of aircraft sheetmetal work, stick with poppers, at least for this project. When, as the Mechanic-in-Charge, you elect to use a different fastener, the wiser course is to do so only from a position of knowledge. And, in my opinion, everything you read on the internet (including this) should be considered heresy until it can be personally verified.
Despite the above warning, allow me to offer a bit of experience-based advice: The construction of your Teenie will proceed at a faster pace if you keep in mind the fact Cal's little bird has been flying - safely - for more thirty years. (You can verify that by public records -- his hull number is N2861.) That means there really isn't a lot the rank novice can do in the way of 'improvements.' So quell the urge.
That tenure of service is good evidence that, as designed, the Teenie Two has more than adequate strength. Indeed, in some areas it is far stronger than required. This too may be verified using public records by reviewing the Teenie's accident statistics.
There are some areas of the Teenie's construction that will require your closest attention but on the basis of strength and safety, fasteners is not one of them.
-R.S.Hoover
- - - - - - - - - - - - - - - - - - - - - - - - - - - - - - - - - - - - - - - - - - - - - - - - -
Note: This message was originally posted to the T2 mailing list several years ago. It is being reposted on rah because questions about poppers keep popping up in my mail box.
No comments:
Post a Comment